CI Type Flexo Printing Machine
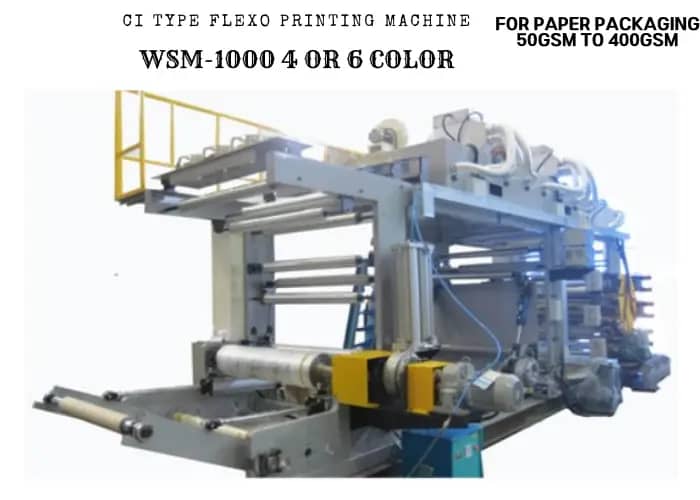
Feature
There are three types of flexo printing machines: stack type, line type, and CI type. The stack type flexo printing machine is generally priced lower than the others; however, it has limitations regarding speed and paper tension, which are weaker compared to the line type and CI type. For spot printing with the line type, it typically does not pose a significant problem; however, the line type flexo printing machine has a critical weakness concerning precise focus. This issue frequently arises in CMYK printing, as certain colors may not focus well due to the extended printing process, where each unit produces a separate color, and the machine’s height is also low. It is challenging to maintain high tension, and there is insufficient drying space.
The CI type has the largest machine size compared to the other types. While a line type with full electronic options and various features can exceed that of a CI type, generally, the CI type flexo printing machine is the largest, and it typically boasts the fastest printing speed. Additionally, its paper tension is stronger than that of other types of printing machines. Due to the drying system, the machine’s size inevitably becomes larger. Thus, in our opinion, the best choice among the various types of flexo printing machines is the CI type.
However, it is true that CI type flexo printing machines are extremely expensive due to the numerous electronic components and automatic systems that significantly drive up the price. In order to provide our printing machine at a reasonable price, we must eliminate automatic systems, as these predominantly cause the price to exceed millions of dollars.
By removing the automatic systems, while still maintaining the benefits of the CI type, we need to focus on a mechanical system that ensures a reasonable price and avoids technical issues that can arise from complex electronic systems.
However, our WSM1000 is not a fully manual system. It features a paper tension controller communicating between the Unwinder and Rewinder, an automatic stop system in case of paper disconnection, and paper reel adjustment to rewind the paper roll correctly, which are fully automatic.
The construction of the WSM1000 is notably simple, except for the size of the parts, making the machine quite large. Anyone can maintain this machine and easily troubleshoot, as there is rarely an occurrence of malfunction due to the mechanical construction. Most malfunctions arise from electronic and electrical systems. So, in the future, after installation, this machine will help users avoid any headaches from malfunctions. Moreover, there are no special consumable parts, and no unique spare parts are required. Most components can be used until the machine reaches the end of its life many years later.
The only systems present in our machine are an automatic paper tension system and an electronic paper reel adjusting system. These systems suffice for printing; any additional optional equipment is merely for convenience. You will need to decide whether you prefer to manage the inconvenience of adjusting the focus mechanically to keep your investment low or if you prefer the convenience of controlling everything with a computer system, which will involve a much higher investment. Even without the optional electronic system, you should not face any significant inconvenience; you will be able to meet acceptable standards. The key systems that ensure good quality in a flexo printing machine are:
1) Printing speed : This allows you to utilize high-fidelity rubber clichés; if the running speed is slow while using high-fidelity rubber clichés, the print quality will be unsatisfactory.
2) Paper tension : This keeps the paper correctly positioned for printing. If paper tension is insufficient, some colors may experience bounce-back issues.
3) Printing pressure :If printing pressure is unbalanced, one side may appear darker while the other appears lighter.
4) Paper reel adjustment => If the paper reel is not unwound correctly, it can create issues during the die-cutting process and lead to paper damage.
5) Rubber clichés => These are crucial for achieving good printing quality. Regardless of whether a machine operates rapidly or not, you must determine the fidelity (LPI) of the rubber cliché.
6) Ceramic anilox => This transfers ink and determines color tones.
7) Drying :If drying is insufficient, the reverse side of the paper may stick to the ink when the paper is rewound. However, this issue could happen if the ceramic anilox is incorrectly chosen by the user for two-sided PE coating, even with very expensive machines.
If all the aforementioned factors are well-coordinated, you should not encounter issues in producing high-quality prints.
Therefore, having intricate electronic equipment can lead to significant complications if any electronic components fail. Our machine is simple but large in size due to its speed and drying system. If you utilize our machine, you will not face severe problems, nor will you have to deal with complex electronic systems. Many individuals actually prefer mechanical systems over electronic ones due to maintenance concerns.
Specficication
-Max. Printing width: 1000 mm
-Max. Printing speed: 110 m per min
-Electric power requirement: 60 kW
-Ink dries by hot air
-Two chambers of hot air box, one chamber for each color, and one central drying chamber
-Equipped with an automatic paper tension controller
-Automatic EPC paper reel rewinder controller
-Includes a corona coating treatment system
-Size: L 12 meters, H (4 colors) 3 meters, H(6 colors) 4 meters, W: 2.5 meters
-Printing material: from 50 to 400 gsm paper for heavy weight paper packaging